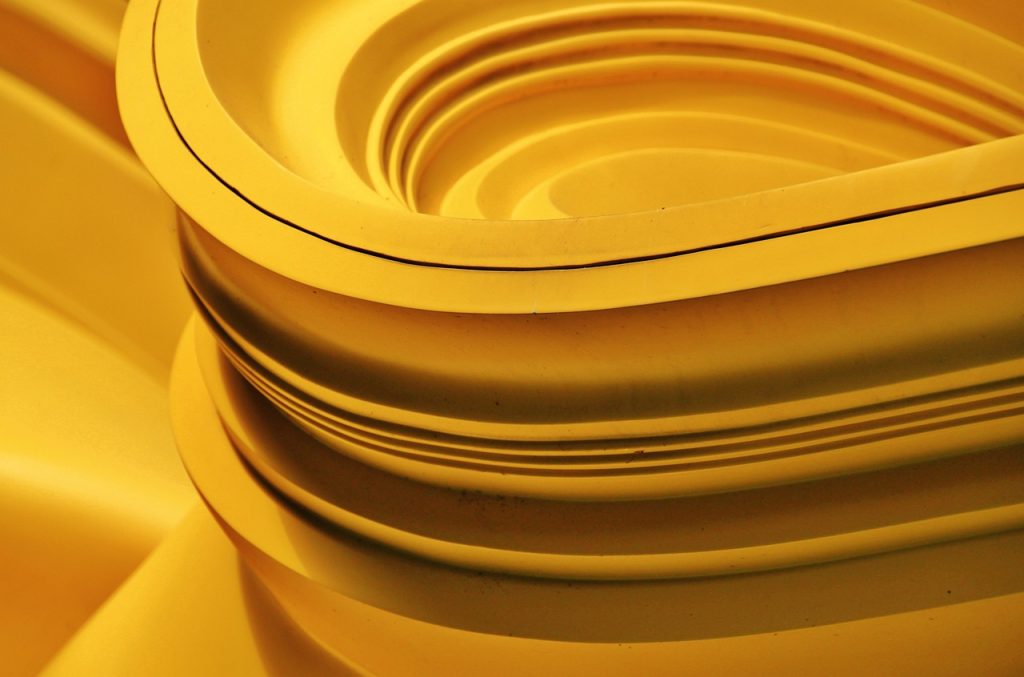
Thermoforming is a manufacturing process that involves heating a plastic sheet until it becomes pliable, then shaping it into a specific form using a mold. This technique is widely used in various industries, from packaging to automotive, due to its versatility and cost-effectiveness. In this article, we’ll explore the benefits of thermoforming plastic and materials and why it’s a preferred method for producing a wide range of products like railing decor for outdoor steps.
Versatility in Design and Application
Thermoforming offers the advantage of producing custom shapes and sizes. It can accommodate many specifications, from intricate designs to large thermoforming plastic panales or small components, making it suitable for manufacturing medical trays, food packaging, automotive parts, and consumer goods. Thermoforming is compatible with various plastic materials such as ABS, PET, polycarbonate, and acrylic.
Each material offers different properties, allowing manufacturers to select the best option for their specific application, considering factors like durability, transparency, and impact resistance.
This versatility in materials expands the possibilities for product design and functionality. Thermoforming provides a wide range of color and texture options, including glossy, matte, or textured finishes. It also allows for adding color during manufacturing, eliminating the need for post-production painting or coating.
Cost-Effective Manufacturing
Thermoforming offers several advantages over other manufacturing methods. First, it involves lower tooling costs compared to methods like injection molding. The molds used in thermoforming are generally less expensive to produce, especially for large or complex parts, making it an attractive option for both small and large production runs. Additionally, thermoforming is known for its efficient production process.
Once the molds are created, the forming of the plastic sheets is relatively quick, allowing for high production rates. This efficiency results in lower labor costs and faster turnaround times, making thermoforming an economical choice for many manufacturers.
Furthermore, thermoforming is a material-efficient process that minimizes waste during production. The plastic sheets can be precisely cut to fit the mold, and any excess material can often be recycled or reused, reducing overall material costs and supporting sustainable manufacturing practices.
- Precision and Detail: Thermoforming allows for high precision and detail in the final product. The process can produce sharp edges, intricate patterns, and detailed textures that are difficult to achieve with other methods. This level of detail is particularly important for products that require a high-quality finish, such as consumer electronics or medical devices.
- Consistency and Uniformity: One of the key benefits of thermoforming is its ability to produce consistent and uniform products. The use of molds ensures that each part is identical, which is crucial for applications where precision and consistency are essential. This uniformity also simplifies the assembly process for products with multiple components.
- Durability and Strength: Thermoformed products are known for their durability and strength. Thermoformed parts can be resistant to impact, chemicals, and UV radiation depending on the material used. This makes them suitable for various demanding applications, from outdoor signage to automotive interiors.
Eco-Friendly Options
Thermoforming is an environmentally friendly manufacturing option. It allows for the recycling of materials like PET and HDPE. It is also more energy-efficient and produces less waste than other plastic-forming processes.
The Advantages of Thermoforming
Thermoforming offers a range of benefits that make it an attractive manufacturing method for various industries. Its versatility in design, cost-effectiveness, high-quality results, and eco-friendly options set it apart from other plastic forming techniques. Whether you’re looking to produce custom parts, packaging, or consumer products, thermoforming provides a reliable and efficient solution that meets the demands of modern manufacturing.